Improvement of the mapping accuracy in the material modeling by considering the yield locus under plane strain
Head
Researcher
Funding period:
Start: 1. April 2023
Ende: 31. March 2025
Abstract
Nowadays, forming processes are analyzed, evaluated and designed using simulation. Precise material modelling is an important factor in improving the mapping accuracy of a forming process in the simulation. Due to the growing computing power and increasing progress in material characterization, material models with a high number of degrees of freedom can be used. In contrast a huge number of tests are required.
Conventional material models, such as Hill'48, Yld2000-2d or BBC05, are implemented in commercial FE software and offer comparatively short calculation times. However, these material models cannot directly model the stress states of plane strain and shear. These are only approximated on the basis of the input data and therefore are subject to a high degree of scatter. In the first project phase, it was demonstrated that the integration of the real material behavior under plane strain in the rolling direction significantly improved the accuracy of the simulation. Now the quality of the prediction is to be analyzed by implementing additional characteristic values, such as the plane strain perpendicular to the rolling direction or the shear stress. The yield locus exponent offers great potential for this, as it is determined as a function of the material without reference to the laws of metal physics. The roundness of the yield locus curve can be varied by the yield locus exponent, whereby an additional material parameter can be integrated into the material modelling (see figure).
In addition, it is to be investigated whether parameter identification at increased true plastic strains leads to an improvement in the mapping accuracy between numerically calculated and experimentally produced components in the case of distorsionally hardening materials. With the aid of a subroutine, all material parameters are modelled as a function of strain. Finally, the determined yield loci are to be verified and evaluated using two demonstrator components, a cruciform cup and a B-pillar.
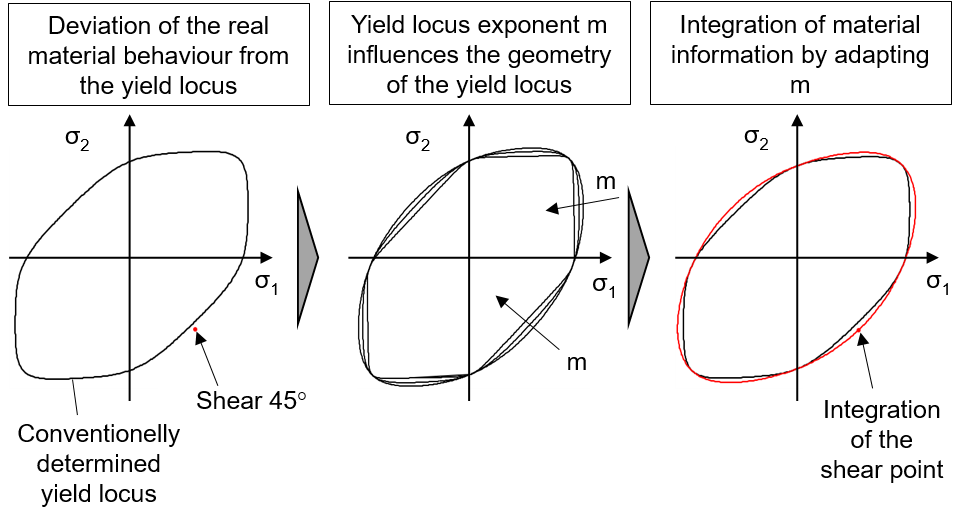